The 9-Second Trick For Alcast Company
The 9-Second Trick For Alcast Company
Blog Article
Alcast Company for Beginners
Table of ContentsSome Known Details About Alcast Company Alcast Company Can Be Fun For AnyoneAlcast Company Things To Know Before You Get ThisSome Known Factual Statements About Alcast Company The Ultimate Guide To Alcast CompanyThe Ultimate Guide To Alcast Company
Chemical Comparison of Cast Aluminum Alloys Silicon promotes castability by reducing the alloy's melting temperature and improving fluidness during casting. Furthermore, silicon adds to the alloy's toughness and put on resistance, making it beneficial in applications where durability is important, such as automotive components and engine components.It additionally boosts the machinability of the alloy, making it simpler to process into ended up items. In this way, iron contributes to the total workability of aluminum alloys.
Manganese contributes to the strength of aluminum alloys and boosts workability (aluminum foundry). It is generally used in functioned aluminum products like sheets, extrusions, and profiles. The presence of manganese aids in the alloy's formability and resistance to cracking during fabrication processes. Magnesium is a lightweight component that provides strength and effect resistance to aluminum alloys.
Examine This Report about Alcast Company
It enables the production of light-weight parts with superb mechanical residential properties. Zinc boosts the castability of light weight aluminum alloys and helps control the solidification process throughout spreading. It improves the alloy's toughness and hardness. It is usually found in applications where elaborate forms and great information are essential, such as decorative castings and certain automotive parts.

The key thermal conductivity, tensile strength, yield strength, and elongation differ. Among the above alloys, A356 has the greatest thermal conductivity, and A380 and ADC12 have the most affordable.
Get This Report on Alcast Company
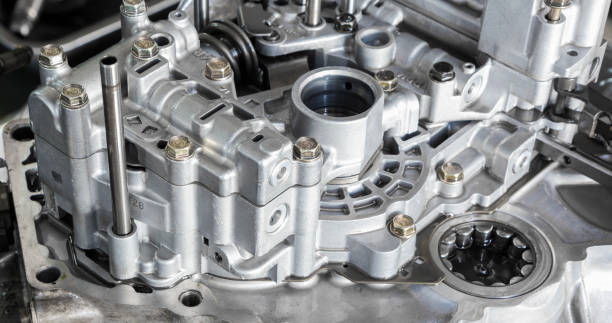
In precision casting, 6063 is fit for applications where detailed geometries and high-quality surface area finishes are critical. Examples consist of telecommunication units, where the alloy's remarkable formability enables streamlined and cosmetically pleasing styles while preserving structural honesty. In the Illumination Solutions market, precision-cast 6063 parts develop elegant and effective illumination components that need detailed forms and good thermal performance.
The A360 displays remarkable elongation, making it perfect for facility and thin-walled parts. In accuracy casting applications, A360 is well-suited for sectors such as Customer Electronic Devices, Telecommunication, and Power Devices.
About Alcast Company
Its unique properties make A360 a beneficial selection for accuracy casting in these markets, boosting item sturdiness and top quality. aluminum foundry. Aluminum alloy 380, or A380, is a widely used spreading alloy with several distinctive qualities.
In accuracy spreading, light weight aluminum 413 shines in the Consumer Electronics and Power Devices sectors. It's typically utilized to craft intricate components like mobile phone real estates, video camera bodies, and power tool casings. Its accuracy is remarkable, with tight resistances approximately 0.01 mm, making certain perfect item assembly. This alloy's superior rust resistance makes it an excellent selection for outside applications, guaranteeing durable, resilient products in the pointed out sectors.
More About Alcast Company
The light weight aluminum alloy you select will considerably impact both the casting process and the buildings of the last item. Because of this, you should make your decision very carefully and take an enlightened strategy.
Determining the most appropriate aluminum alloy for your application will suggest weighing a large array of characteristics. The very first classification addresses alloy qualities that affect the production procedure.
Alcast Company Fundamentals Explained
The alloy you pick for die spreading directly influences numerous facets of the spreading procedure, like learn the facts here now just how simple the alloy is to collaborate with and if it is prone to casting issues. Hot splitting, likewise referred to as solidification breaking, is a common die casting defect for aluminum alloys that can result in interior or surface-level splits or cracks.
Certain aluminum alloys are a lot more susceptible to hot fracturing than others, and your choice must consider this. It can harm both the actors and the die, so you should look for alloys with high anti-soldering residential properties.
Deterioration resistance, which is currently a noteworthy quality of light weight aluminum, can differ considerably from alloy to alloy and is a vital particular to take into consideration depending on the ecological conditions your product will certainly be revealed to (Casting Foundry). Wear resistance is an additional building frequently sought in light weight aluminum items and can set apart some alloys
Report this page